The revolution will be 3D printed
Imagine a world in which gadgets aren't made by hand or constructed by robots, but printed – in one piece – in your room. It's coming
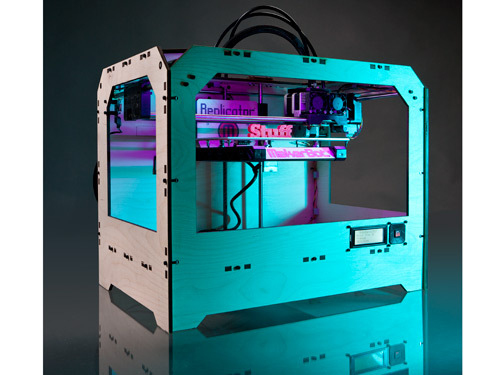
Holodecks, hoverboards, gravity guns – just a few of the sci-fi gadgets that are still sadly missing from our lives. But fear not, there is one fictional tech that’s about to enrich our reality – the Star Trek replicator. Its real-world equivalent, 3D printing, can’t yet rustle up a baguette from thin air, but in the next few years it’s going to send shockwaves through manufacturing and change the way you buy things. Bespoke products will become the norm, and you need never struggle to get your hands on a spare part again. But it won’t be good news for everyone.
Physical products being replaced by digital files? We’ve been here before, as the music industry will attest. And as it discovered, ones and zeroes are a lot easier to copy and distribute than atoms. For some, the threat of 3D piracy lurks in these uncharted waters – but for us, an exciting personalised future awaits…
The pioneers
MakerBot Industries
Founded three years ago, this New York company has been the pioneer of open-source 3D printers – starting with the DIY Thing-O-Matic 2010, and this year following up with the pre-built MakerBot Replicator.
Cubify
The makers of the Cube 3D printer also offer an online store that lets ‘Cubify artists’ upload and sell 3D designs or, like Sculpteo and Shapeways, get models printed using its Cloud 3D Print Service.
Sculpteo
This French service lets you design or upload 3D creations to its site in most file formats, then pops a tri-dimensional version in the post to you. An iOS app also lets you cut your teeth by customising a selection of objects from its favourite designers.
Organovo
Leading the way in the mildly terrifying field of ‘bioprinting’, this San Diego-based startup has 3D-printed muscle, lung and blood vessel tissue and has its sights set on making complete organs for transplants.
From the start
3D printing – or additive manufacturing, to give its official title – first appeared in the early 1980s. Simply put, it’s the process of creating an object by building up layers of material, rather than by taking a block of raw material and carving shapes out of it.
3D printers use a variety of techniques for layering different materials – home hobby devices like MakerBot’s Replicator extrude plastic, while industrial setups like Objet use an inkjet head to spray UV-sensitive plastic before curing it with UV light. Other printers use laser sintering to fuse layers of powdered metal. Designer Enrico Dini has even created an architectural 3D printer that can produce entire buildings from sandstone.
The technique may vary, but the result is the same – an extremely cool technology that’s potentially the most revolutionary since the birth of the internet.
Homeward bound
In the early days, 3D printers were huge – and expensive. But they’ve been getting progressively smaller and more efficient, and we’re now reaching a point where 3D printers like the Cube and MakerBot are available for us to buy.
“Look at 2D printing,” says Robert Jeffries, 3D technical specialist at Inition. “For a very long time you used to have to go to a reprographics centre to get prints done, because you just couldn’t afford a printer. I think the next wave of 3D printing is more accessible bureau centres, so that in every part of a city or town there’ll be a place you can go to get 3D prints. Eventually it will filter down to the home.”
Today, home 3D printers are the preserve of geeks and hobbyists – and the low-definition plastic objects, with their ridged, blocky layers of plastic, are mainly curios. But the tech is only going to get more sophisticated.
Impossible structures Already, 3D printing is helping manufacturers create objects that they previously couldn’t. When building Concorde, aircraft engineers had to painstakingly mill aluminium to create components with cavities that would reduce weight while retaining strength.
With modern 3D printing techniques, companies like EADS Innovation Works are creating intricate, lightweight metal components that couldn’t be created using carving or moulding processes. British bike company Charge has already made dropouts (the bit your bike’s real wheel attaches to the frame), hinting at the imminent possibility of a 3D-printed bike.
It’s even possible to create working machines using 3D printers. “There’s almost no geometry that we can’t print,” says says Objet’s European head Andy Middleton. “I have this example on my desk – 24 gears that fit into each other in a spherical shape, with no assembly taking place at all. It’s an almost insurmountable task for conventional methods.”
“You see some fantastic things, like tables and stools that can fold and change shape – and they’re all printed in one piece,” says Robert Jeffries of Inition. “There is no way of doing that other than 3D printing.”
Supply and demand 3D printing is about to turn manufacturing on its head too. Conventional manufacturing methods like injection-moulding need large production runs. But with 3D printing you can produce a much smaller number of products, opening the door for people to produce personalised items for a more limited audience.
3D printing services like Shapeways, Cubify and Sculpteo are springing up, letting you upload 3D printing files and have your objects produced in a professional 3D printing setup. These sorts of local 3D printing services are good for the environment, too – businesses don’t have to ship products from overseas manufacturing plants, they can just ping 3D files to regional plants for local manufacture and distribution.
Spare parts 3D printing also does away with the need for warehouses full of spare parts. If, say, your washing machine breaks, the manufacturer can just send you the 3D printer file for the relevant component, and you can take it to a 3D printing service – or even print it yourself.
“People have created spare parts for a coffee machine,” says Clement Moreau, director of Sculpteo. “The surprise is that spare part has been available as a public object on the website and it’s been reordered by other people.”
But don’t go thinking you can just print off your own spares for anything. “That assumes many things,” says Andy Middleton. “One: that the specifically approved materials are available. The second one is, how does that affect the manufacturer’s warranty or guarantee on that part?” “The next step will be that brands will finally understand that they don’t need to create spare parts by themselves, they just need to push the 3D file on one of the platforms,” says Moreau.
Personal products One of 3D printing’s most exciting features is the ability to create bespoke, customised products. Already, firms like Sculpteo and Shapeways let you add a personal touch to products – you can pop an image of your profile on a mug, or turn a sound wave into a customised iPhone case. A bit gimmicky? Sure, but the possibilities are endless. 3D printing has even been used to create a customised jaw transplant for a woman who’d had part of her jaw removed due to cancer – surely the ultimate bespoke item.
Of course, there will still be a place for designers – most of us don’t know about mechanical stress and tolerances, or have the artistry required to design a product. “Even if 3D printing gives you the right tools, it doesn’t make you a designer,” says Clement Moreau of Sculpteo. But the relationship between you and the product designer will change.
“The designers will be more of a service to the buyer,” says Andy Middleton. “Rather than the designer saying, ‘This is the design, take it or leave it,’ it will change to the customer saying, ‘This is what I want, can you do it for me?’ So the balance will shift to the consumer.” Take that, Jonathan Ive.
Let’s get physible
Beyond revolutionising the Christmas present, 3D printing’s biggest impact will arguably be to turn many manufacturers from traders in physical products to information brokers. Their key resource will not just be the products they sell – it will be the information that describes those products. And information can be copied and distributed very easily on the internet.
The Pirate Bay has already sailed into these choppy waters, launching a new section for 3D printer files – or “Physibles,” as the site’s dubbed them. Oddly, one of the first businesses to be affected by the arrival of Physibles is Games Workshop – the chaps who create those little metal orcs and goblins for tabletop wargames (don’t pretend you don’t remember).
In 2011, it discovered that someone had been creating tanks and Space Marines for Warhammer 40,000 that were based on the company’s designs and sharing them on the 3D printing website Thingiverse. Games Workshop swiftly moved to shut down the pirates, stating that “We are very protective of our intellectual property.” Almost exactly the same response as that of the record companies when confronted with Napster, then.
Copyright infringement – copying a creative work – is only the start of it. When home 3D printers become sophisticated enough to create working machines, users will start having to worry about patent infringement.
Patently disruptive
If you thought the patent wars around big corporations like Apple and Samsung were holding innovation back, just wait until the patent trolls start targeting ordinary folks who’ve unwittingly infringed patents with their home 3D printers.
“A lot of industries that are focused on making physical things are going to be confronted with a very similar dilemma to that faced by creative industries in the last 10 years – there is going to be a new way to distribute their key product,” Michael Weinberg, author of the white paper “It will be awesome if they don’t screw it up”, tells Stuff. “They can spend a lot of time and money fighting that change, or they can spend even less time and money making use of that change.”
Stuff Says
The seismic digital waves that have swept through the music and movie industries are starting to rumble manufacturing – and will ultimately have the same revolutionary impact. As 3D printers become more widespread, copyright and patent infringement wrangles will grow – and only manufacturers willing to embrace it will survive. For them, it’s disruptive change – but for us, a brave new world of personalised products and collaborative design awaits. Not to mention some really amazing Christmas presents.
You may also like